View previous topic :: View next topic |
Author |
Message |
wilsteadt
Joined: 15 May 2010 Posts: 27
|
Posted: Sun Oct 03, 2010 11:19 pm Post subject: Hull welding |
|
|
I have decided to add some extra plating to my hull and have some questions. My preferred welding method is TIG but I have absolutely no luck on the bottom of my boat. I assume that this is due to the corrosion. I use a flap disk and a SS wire brush but still just make a mess. I can do a decent job with TIG'ing in my shop in any direction and even on relatively dirty material but have never been able to do much more than make a mess on my hull. I even have more of a problem with MIG under the hull. It may just be that I suck at over head welds?
My hull has been used in salt water and I don't know if this allows corrosion to penetrate the aluminum more and could be causing my problems.
Any advice would be appreciated.
Also, does anyone with a high frequency TIG have issues with their flouresent lights while welding?
Thanks,
Matt |
|
Back to top |
|
 |
JR
Joined: 23 Jul 2005 Posts: 81
|
Posted: Mon Oct 04, 2010 8:09 am Post subject: Re: Hull welding |
|
|
wilsteadt wrote: | I have decided to add some extra plating to my hull and have some questions. My preferred welding method is TIG but I have absolutely no luck on the bottom of my boat. I assume that this is due to the corrosion. I use a flap disk and a SS wire brush but still just make a mess. I can do a decent job with TIG'ing in my shop in any direction and even on relatively dirty material but have never been able to do much more than make a mess on my hull. I even have more of a problem with MIG under the hull. It may just be that I suck at over head welds?
My hull has been used in salt water and I don't know if this allows corrosion to penetrate the aluminum more and could be causing my problems.
Any advice would be appreciated.
Also, does anyone with a high frequency TIG have issues with their flouresent lights while welding?
Thanks,
Matt |
With The Lights you will need to have the right filler wire ... Sorry i just had to...
By the sounds of it you have had a real good clean before you weld... Are you getting enough heat in before you start your bead... Try to run a weld on the new stuff first this will tell you if it is the old part of the hull has still got salt on/in it... Cheers JR _________________ Life is Short, Play the cards you get, Go Hard or Go Home..... |
|
Back to top |
|
 |
boosted
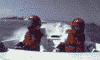
Joined: 04 Jun 2009 Posts: 378
|
Posted: Mon Oct 04, 2010 8:41 am Post subject: |
|
|
Enough heat for Tig is esssential. You should be using close to 300 amps to weld that. You should also preheat that a little with a torch. Don't get it to hot though as once you get close to 600 deg if it is heat treated aluminum then it will start to loose strength. In that application a good mig weld is actually better. _________________ Mark
Lets go back I think we missed one rock! |
|
Back to top |
|
 |
|